Case Study: How VelociBuilders Streamlined a Complex Holiday Shipping Operation
Introduction to VelociBuilders' Challenge
As the holiday season approached, VelociBuilders, a leading e-commerce construction tools supplier, faced a daunting challenge. The annual spike in demand meant they needed to streamline their shipping operations to ensure timely delivery of orders. With a complex logistics network and the pressure of holiday deadlines, VelociBuilders turned to innovative solutions to enhance their shipping efficiency.
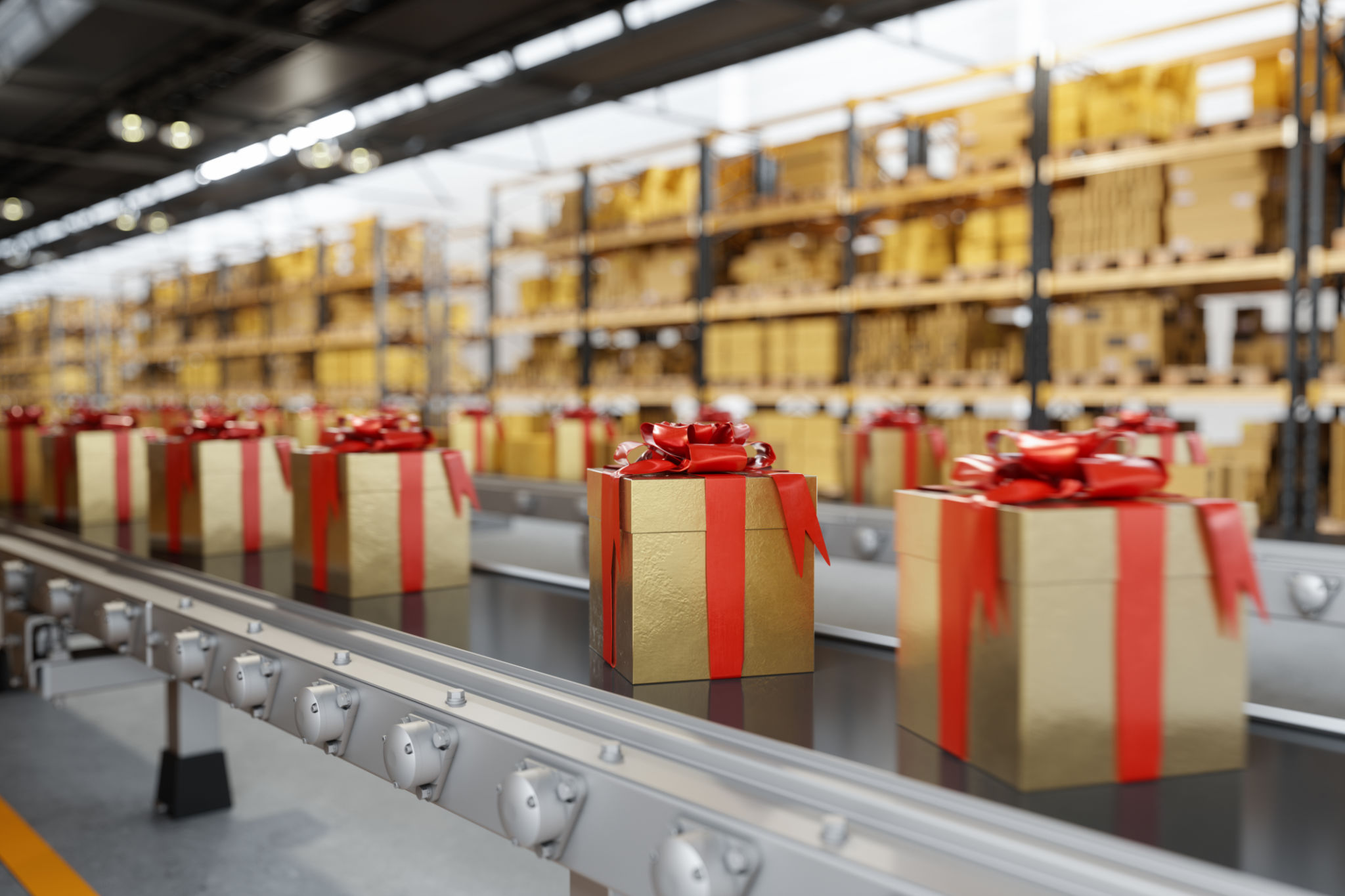
Identifying the Pain Points
Before implementing new solutions, VelociBuilders conducted a thorough analysis of their existing shipping process. They identified several key pain points: bottlenecks in order processing, delays in warehouse operations, and inefficiencies in last-mile delivery. Understanding these challenges was crucial to developing an effective strategy.
The team discovered that manual order processing was causing significant delays. Additionally, the warehouse layout was not optimized for peak season operations, leading to longer picking and packing times. Last-mile delivery was also hindered by inadequate route planning, resulting in late deliveries and dissatisfied customers.
Implementing Technology-Driven Solutions
To address these issues, VelociBuilders invested in state-of-the-art technology. They implemented an automated order processing system that reduced human error and accelerated order throughput. By integrating this system with their existing ERP software, they achieved real-time inventory tracking and seamless communication between departments.
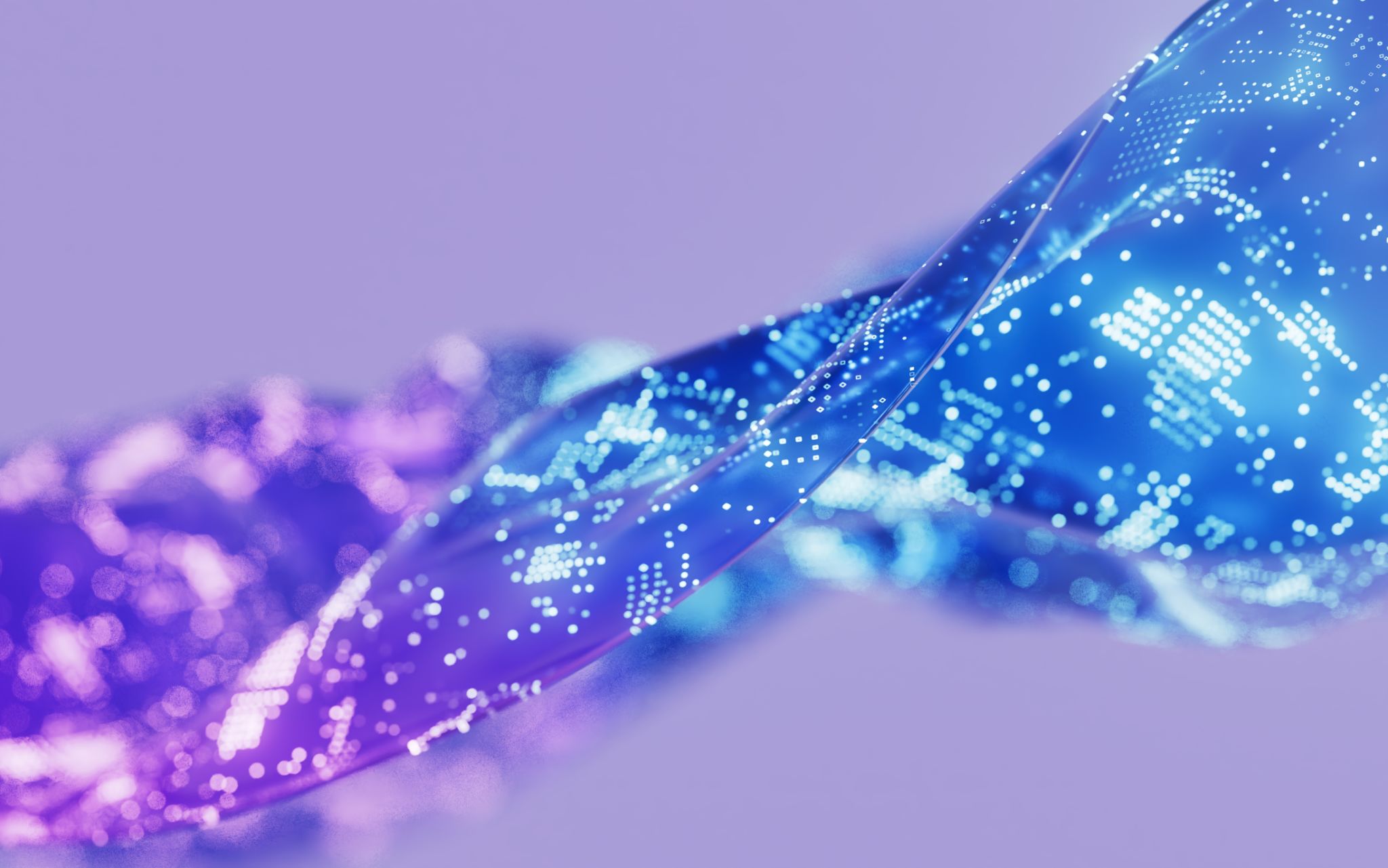
The warehouse was restructured using a data-driven approach, optimizing the layout for efficiency. This included reorganizing product placement based on order frequency and utilizing automated guided vehicles (AGVs) to assist in moving goods quickly across the facility. These changes significantly reduced picking and packing times.
Enhancing Last-Mile Delivery
Improving last-mile delivery was another crucial aspect of VelociBuilders' strategy. They employed advanced route optimization software to plan the most efficient delivery routes. This software considered variables such as traffic patterns, delivery windows, and vehicle capacity to minimize fuel consumption and delivery time.
Furthermore, VelociBuilders expanded their delivery fleet to include electric vehicles, aligning with their commitment to sustainability. This not only reduced environmental impact but also allowed for more flexible delivery options during peak hours.
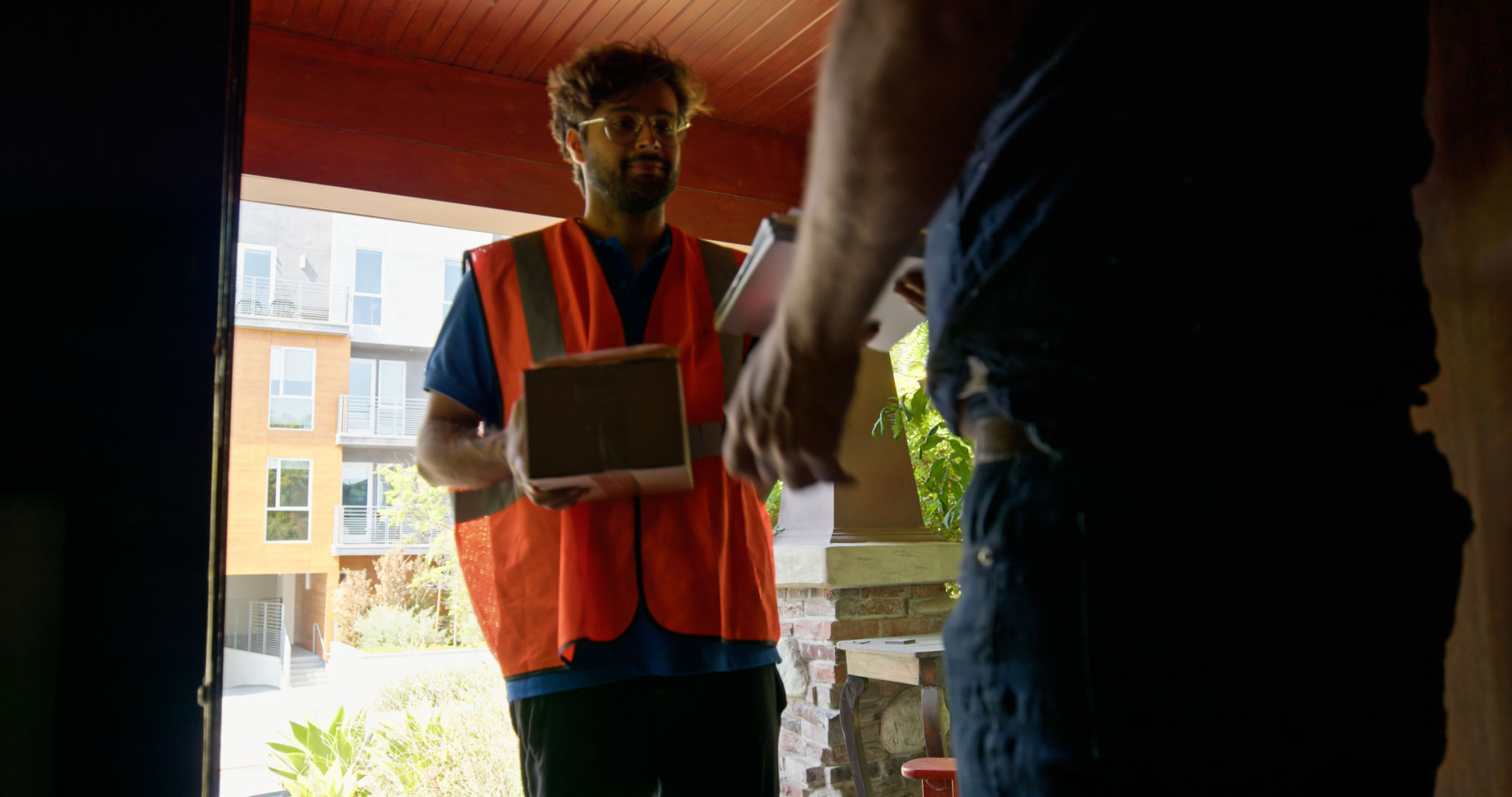
Results and Customer Satisfaction
The impact of these changes was profound. VelociBuilders reported a 30% increase in shipping efficiency and a 20% reduction in delivery times during the holiday season. Customer satisfaction soared as timely deliveries became the norm rather than the exception. Positive feedback from clients highlighted the reliability and speed of their service.
The company's proactive approach in adopting new technologies and optimizing their operations not only improved their bottom line but also strengthened their reputation as a customer-centric brand.
Lessons Learned
VelociBuilders' experience provides valuable insights for other businesses facing similar challenges. One key takeaway is the importance of identifying bottlenecks early and addressing them with targeted solutions. Embracing technology can lead to significant improvements in efficiency and customer satisfaction.
Additionally, being adaptable and willing to invest in sustainable practices can offer long-term benefits both environmentally and economically.
Conclusion
The successful transformation of VelociBuilders' holiday shipping operations serves as an inspiring case study for businesses looking to streamline complex logistics. By investing in technology and optimizing processes, companies can not only meet but exceed customer expectations during peak seasons. As demonstrated by VelociBuilders, innovation and efficiency go hand in hand in today's competitive market landscape.